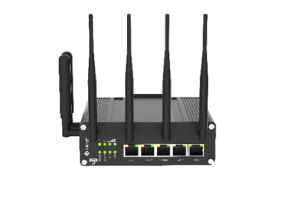
Fig. WiFi router
In the marine sector, WiFi is primarily known for providing Internet access using routers on boats. Wifi is based on the 802.11 bgn standard and uses 2.4 GHz frequencies. With 802.11 ac, frequencies with 5 GHz and 6 GHz are also possible, which enable higher data rates. Modern plotters can transmit some information to mobile devices and use WiFi for this.… Continue reading
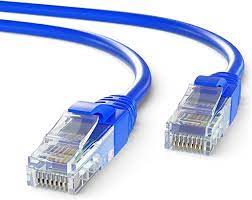
Ethernet is the well-known connection technology in the computer sector, which is very robust and fail-safe due to the galvanic decoupling of the end devices. Ethernet connections enable transmission speeds between 10Mbit/s up to 10GBit/s. Shielded 2-wire lines or fiber optic cables can be used as the transmission medium. RJ45 plugs have established themselves as connectors for cable connections, but they are not suitable for marine applications in humid environments.… Continue reading
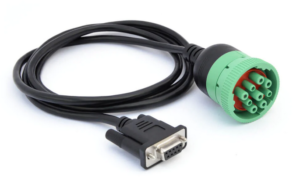
Fig.: J1939 connection technology
J1939 is mainly used in the automotive sector to network components in order to reduce the wiring effort. It is based on the CAN bus as a transmission method. J1939 was approved by the international Society of Automotive Engineers (SAE) defines and works on the physical layer with CAN high-speed with 1 MBit/s. In the marine sector, the CAN speed was reduced to 250kBit/s to enable a certain degree of compatibility with NMEA2000.… Continue reading
SeaSmart is a group of protocol implementations of different bus types, for the uncomplicated data exchange between marine devices from the company Digital marine gauges was developed. SeaSmart focuses on the transmission and display of boat information, especially over Ethernet and WiFi connections. Web browsers serve as display devices, which receive their data from special gateways from SeaSmart.Net. SeaSmart is not very common and more of a niche product.… Continue reading
With SignalK an attempt was made to create an alternative to established commercial boat bus systems based on open source. The aim is to consolidate a wide variety of sensor data from different bus systems and integrate them into a uniform, flexible and expandable data model, comparable to open source solutions in home automation. SignalK takes on several tasks. On the one hand, data from a wide variety of vehicle electrical systems is processed and, on the other hand, there is the option of visualizing the data individually via websites.… Continue reading
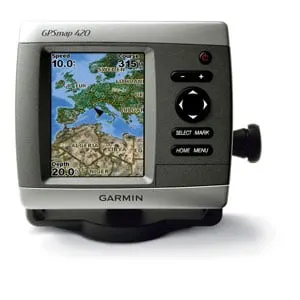
Fig.: GPSmap 420 with CANet (Garmin)
CANet was developed by Garmin for marine devices. It uses the CAN bus at the lowest physical level, but uses different implementations at higher levels of CAN and is not compatible with NMEA2000. Like C-Net 2000, CANet is a proprietary protocol that only works with Garmin devices. Many older Garmin plotters were equipped with CANet and NMEA0183.… Continue reading
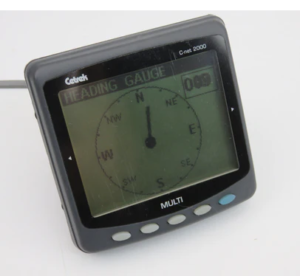
Fig.: Ctrec C-Net 2000
C-Net 2000 was developed by Cetrek for marine devices. It uses the CAN bus at the lowest physical level, but does not use any higher level implementation of CAN. C-Net 2000 is therefore a proprietary protocol that only works with Cetrek devices. Many Cetrek display devices include a gateway for NMEA0183 and C-Net 2000 so that data can be exchanged between the networks.… Continue reading
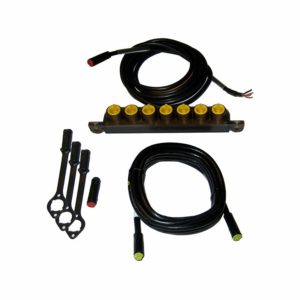
Fig.: SimNet connection technology
SimNet is a bus system for boats from Simrad, which is based on the CAN bus and has limited compatibility with NMEA2000, comparable to Raymarine's SeaTalk NG. With SimNet, Simrad also relies on proprietary connection technology that is only compatible with Simrad products. Physically, 5-pin connectors are used as in NMEA2000, but in a different format.… Continue reading
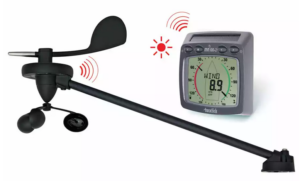
Fig.: Masttop transducer T120 (Raymarine)
MicroNet is a wireless sensor data transmission method supported by some Raymarine sensors and displays, such as the T120 masthead wind transducer and the Log + Echosounder system in conjunction with the Marine TackTick T100 display. Raymarine also offers a gateway called Micro-Talk that can convert data from the wireless MicroNet to SeaTalk NG.… Continue reading